Quy trình đánh bóng sàn gạch là một tiến trình kỹ thuật chuyên nghiệp nhằm nâng cao chất lượng thẩm mỹ và độ bền của bề mặt gạch lát nền. Quy trình này được thiết kế để giải quyết các vấn đề như khuyết tật bề mặt, độ bóng không đồng đều và tuổi thọ sử dụng của sàn gạch. Bắt đầu với giai đoạn chuẩn bị kỹ lưỡng, bao gồm việc kiểm tra bề mặt bằng đèn LED cường độ cao, vệ sinh sơ bộ và chuẩn bị công cụ chuyên dụng. Tiếp theo là quy trình đánh bóng chính với ba công đoạn: đánh bóng thô (1200-1500 vòng/phút), đánh bóng trung bình và đánh bóng tinh (800-1000 vòng/phút). Trong suốt quá trình này, việc kiểm soát các thông số kỹ thuật như áp lực (3-5kg/cm²) và nhiệt độ (≤40°C) là vô cùng quan trọng để đạt được độ bóng lý tưởng (≥90GU) và đảm bảo bề mặt có độ mịn cấp nhung. Sau khi hoàn thành, công đoạn kiểm tra chất lượng và bảo dưỡng định kỳ sẽ giúp duy trì vẻ đẹp rạng ngời của sàn gạch, kéo dài tuổi thọ và bảo vệ khoản đầu tư của khách hàng.
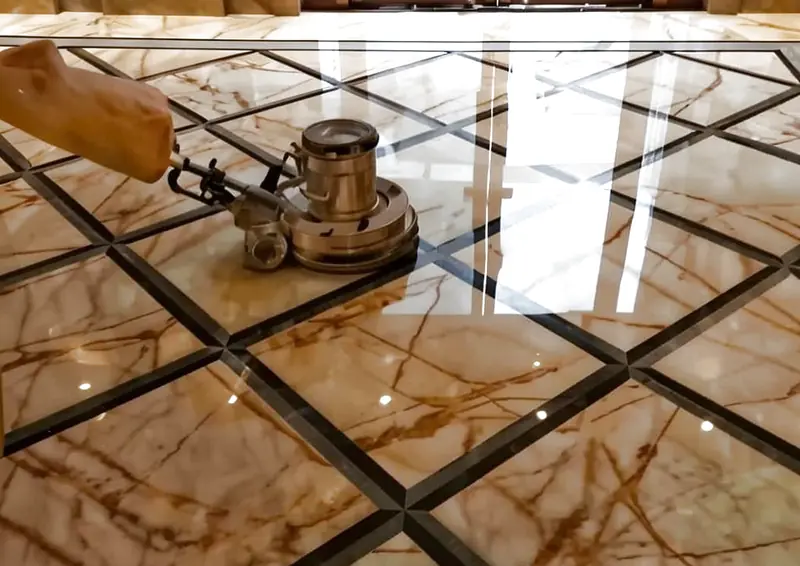
GIAI ĐOẠN CHUẨN BỊ ĐÁNH BÓNG GẠCH LÁT NỀN
Giai đoạn chuẩn bị đóng vai trò quyết định đến 80% thành công của quá trình đánh bóng gạch lát nền. Quy trình chuẩn bị kỹ lưỡng không chỉ nâng cao hiệu quả công việc mà còn giúp phòng tránh các vấn đề phát sinh trong và sau quá trình đánh bóng.
Kiểm tra bề mặt gạch
Đánh giá chuyên sâu bằng kỹ thuật chiếu sáng
- Sử dụng đèn LED cường độ cao (≥1000 Lux) chiếu ánh sáng theo góc 45° so với mặt sàn để phát hiện các khuyết tật bề mặt không thể nhìn thấy bằng mắt thường. Khuyến nghị sử dụng đèn có nhiệt độ màu 5000-6500K để đảm bảo độ trung thực của màu sắc.
- Đánh dấu các vị trí có vết nứt, điểm lồi lõm hoặc khuyết tật men gạch bằng băng dính màu hoặc bút dạ không phai, phân loại mức độ khuyết tật theo thang điểm từ 1-5 (1: nhẹ, 5: nghiêm trọng).
- Thực hiện kiểm tra độ phẳng của bề mặt bằng thước thủy 2m, sai số cho phép không quá 2mm/2m chiều dài. Đối với gạch porcelain, cần kiểm tra kỹ các góc cạnh dễ bị mẻ.
Đánh giá tình trạng khe gạch và độ bám dính
- Kiểm tra độ sâu và tình trạng chất lấp khe, sử dụng dụng cụ kiểm tra độ cứng (thang Mohs) để đánh giá độ cứng của vật liệu lấp khe.
- Gõ nhẹ từng viên gạch để phát hiện hiện tượng gạch bị bong tróc hay không bám dính với nền (tiếng gõ rỗng). Đánh dấu các vị trí này để xử lý trước khi đánh bóng.
- Chụp ảnh toàn bộ bề mặt cần đánh bóng làm tài liệu đối chiếu “trước-sau” và làm bằng chứng về tình trạng ban đầu của sàn, đặc biệt quan trọng đối với dự án thương mại.
Vệ sinh sơ bộ
Loại bỏ bụi và tạp chất
- Sử dụng máy hút bụi công nghiệp có công suất tối thiểu 1800W với bộ lọc HEPA để loại bỏ hoàn toàn bụi mịn, tránh tình trạng bụi bay trong không khí và bám lại trên bề mặt.
- Đối với khu vực rộng trên 50m², nên sử dụng máy quét hút công nghiệp với bàn chải mềm để tránh gây xước bề mặt gạch, đặc biệt với gạch men bóng.
- Với các khu vực góc, khe hở, sử dụng chổi quét chuẩn công nghiệp kết hợp với máy thổi khí nén (áp lực 4-6 bar) để đẩy bụi ra khỏi các khe khó tiếp cận.
Xử lý vết bẩn cứng đầu
- Phân loại các loại vết bẩn: hữu cơ (dầu mỡ, thực phẩm), vô cơ (xi măng, vôi), và kim loại (rỉ sét), mỗi loại cần phương pháp xử lý riêng.
- Đối với vết dầu mỡ: sử dụng dung dịch tẩy rửa gốc kiềm pH 9-11 như dung dịch Xà phòng Marsand FT24 pha theo tỷ lệ 1:10 với nước ấm (40-50°C), thời gian ngâm 15-20 phút.
- Đối với vết xi măng, vôi: sử dụng dung dịch axit yếu chuyên dụng (pH 3-5) như Cleaner AM32, pha loãng theo tỷ lệ 1:5, thời gian tác động không quá 5 phút để tránh ăn mòn bề mặt gạch.
- Sau khi tẩy rửa, cần trung hòa bề mặt bằng nước sạch và kiểm tra độ pH bằng giấy quỳ, đảm bảo pH trở về mức trung tính (6.5-7.5) trước khi tiến hành đánh bóng.
Làm sạch khe gạch
- Sử dụng máy làm sạch khe chuyên dụng với đầu mài oxit nhôm cỡ nhỏ (đường kính 2-3mm) để loại bỏ các chất bẩn trong khe gạch mà không làm hỏng vật liệu chèn khe.
- Đối với khe gạch bị nấm mốc đen, sử dụng dung dịch chống nấm mốc gốc clo (nồng độ 5-10%) kết hợp với bàn chải nylon cứng, chà xát theo chuyển động tròn.
- Sau khi làm sạch, sử dụng máy thổi khí hoặc máy hút ẩm công nghiệp để làm khô hoàn toàn khe gạch, đảm bảo độ ẩm bề mặt dưới 60% trước khi bắt đầu đánh bóng.
- Đối với công trình lớn, cần thực hiện kiểm tra độ ẩm bằng máy đo độ ẩm chuyên dụng tại ít nhất 5 điểm/100m² để đảm bảo độ chính xác.
Chuẩn bị công cụ và vật liệu
Thiết bị đánh bóng
- Máy đánh bóng sàn công nghiệp: có khả năng điều chỉnh tốc độ từ 800-1500 vòng/phút, công suất tối thiểu 1500W cho khu vực thương mại và 800W cho khu vực dân dụng.
- Hệ thống làm mát: bình phun nước điều áp với lưu lượng điều chỉnh 0,5L/phút, giúp kiểm soát nhiệt độ không vượt quá 40°C trong quá trình mài.
- Máy hút bụi đồng bộ: công suất tối thiểu 2000W với bộ lọc nước kép để thu gom bụi mài, đảm bảo môi trường làm việc sạch sẽ.
Vật liệu đánh bóng thô
- Đĩa mài kim cương cỡ hạt 80-120 dùng cho giai đoạn đầu, phù hợp với gạch có độ cứng Mohs 4-6 như gạch ceramic.
- Giấy nhám silicon carbide chịu nước cỡ hạt 120-180, khổ 230mm x 280mm, dùng cho các khu vực góc cạnh máy không tiếp cận được.
- Miếng mài kim cương polyme dẻo dùng cho bề mặt không đồng đều, có khả năng bám dính tốt trên các bề mặt cong.
Vật liệu đánh bóng trung bình
- Giấy nhám cỡ hạt 240-400 với lớp bọt đệm dày 2-3mm, giúp tăng độ linh hoạt khi đánh bóng bề mặt không hoàn toàn phẳng.
- Đĩa mài nhựa resin cỡ 240-320, đường kính 17cm, phù hợp với máy đánh bóng tốc độ 1000-1200 vòng/phút.
- Dung dịch làm mát chuyên dụng không chứa silicone, pha theo tỷ lệ 1:100 với nước để tránh nhiệt độ cao gây nứt gạch.
Vật liệu đánh bóng tinh
- Hạt khô men nhung cao cấp nhập khẩu (loại A+) với kích thước hạt siêu mịn 2-5 micron, dùng cho công đoạn tạo bóng cuối cùng.
- Bánh mài đất tảo cát (diatomaceous earth) kết hợp với sáp tự nhiên, tạo độ bóng sâu và bền màu lâu dài.
- Dung dịch đánh bóng nano với hạt oxit nhôm kích thước dưới 10nm, giúp lấp đầy các lỗ rỗng siêu nhỏ trên bề mặt gạch.
Thiết bị bảo hộ và an toàn
- Khẩu trang N95 hoặc P100 đạt chuẩn NIOSH để ngăn bụi mịn kích thước dưới 2.5 micron gây hại cho phổi.
- Kính bảo hộ kín hai bên với lớp phủ chống đọng sương, bảo vệ mắt khỏi bụi và mảnh vỡ văng bắn.
- Găng tay chống trượt, chống cắt cấp độ 4 theo tiêu chuẩn EN388, giúp bảo vệ tay khỏi vật sắc nhọn và giảm rung khi vận hành máy.
- Nút bịt tai hoặc chụp tai chống ồn có chỉ số giảm ồn (NRR) tối thiểu 25dB để bảo vệ thính giác khi làm việc với máy đánh bóng công suất lớn.
Vật liệu phụ trợ
- Băng keo đánh dấu chịu nhiệt, chống nước để phân vùng làm việc và đánh dấu khuyết tật.
- Thước đo độ bóng góc 60° có độ chính xác ±2GU để kiểm tra chất lượng công việc theo tiêu chuẩn quốc tế.
- Nhiệt kế hồng ngoại đo từ xa với độ chính xác ±1°C để kiểm soát nhiệt độ bề mặt trong quá trình mài.
- Dung dịch độn khe nhanh khô (ron mạch) (thời gian khô 30-60 phút) đảm bảo khe gạch được bảo vệ trong quá trình đánh bóng.
Việc chuẩn bị kỹ lưỡng không chỉ tối ưu hóa hiệu quả công việc mà còn giảm thiểu thời gian xử lý sự cố, tiết kiệm chi phí vật liệu và kéo dài tuổi thọ của thiết bị đánh bóng. Theo thống kê từ các dự án đánh bóng quy mô lớn tại Việt Nam, việc đầu tư 20% thời gian và nguồn lực vào giai đoạn chuẩn bị có thể giảm tới 60% thời gian xử lý sự cố và tăng 40% tuổi thọ của thiết bị.
QUY TRÌNH ĐÁNH BÓNG GẠCH LÁT NỀN
Đánh bóng gạch lát nền đòi hỏi một quy trình chuyên nghiệp, có trình tự và kỹ thuật riêng biệt để đạt được hiệu quả tối ưu. Với quy trình đánh bóng đúng chuẩn, không chỉ bề mặt sàn được phục hồi độ bóng mà còn được bảo vệ và kéo dài tuổi thọ. Quy trình này đòi hỏi sự tinh tế, kiên nhẫn và kiến thức chuyên môn cao.
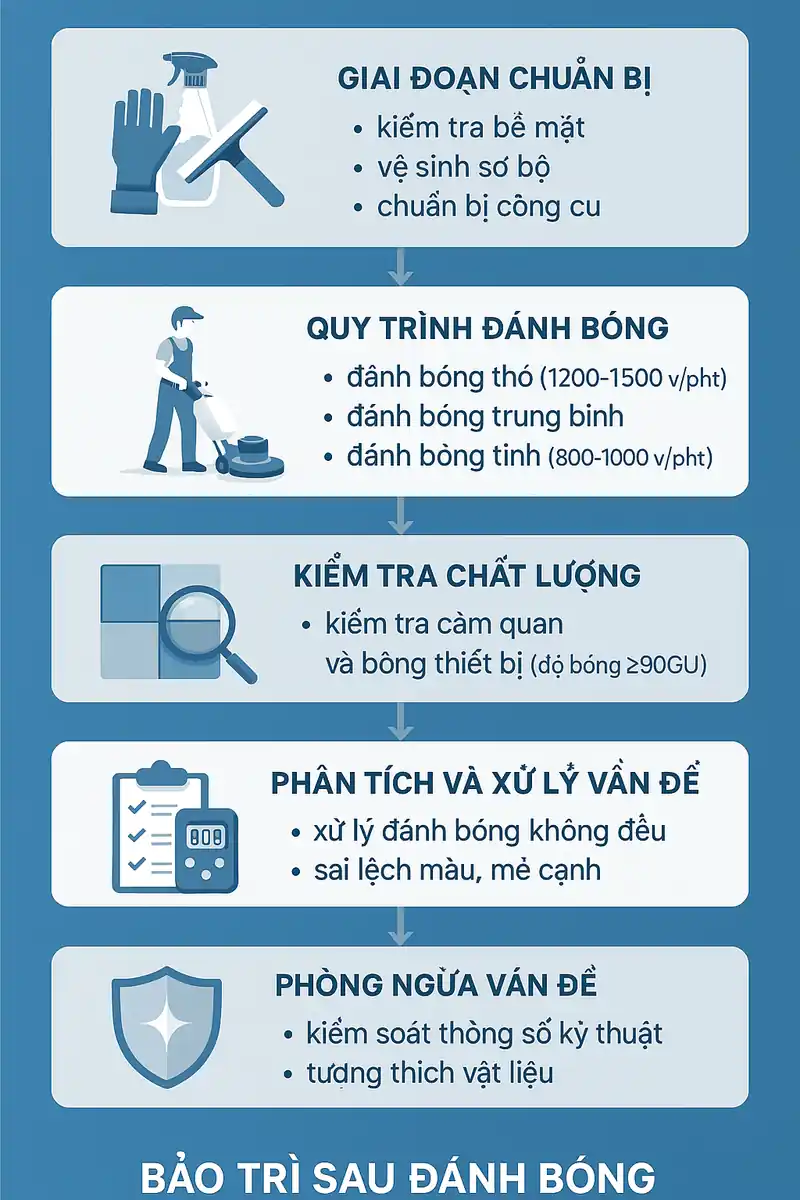
Đánh bóng thô
Chuẩn bị bề mặt trước khi đánh bóng
- Tiến hành quét dọn kỹ lưỡng toàn bộ bề mặt sàn nhằm loại bỏ bụi, cát và các mảnh vỡ nhỏ. Việc này ngăn ngừa các hạt cứng gây xước bề mặt trong quá trình đánh bóng.
- Sử dụng máy hút bụi công nghiệp với công suất tối thiểu 1800W kèm bộ lọc HEPA để đảm bảo loại bỏ triệt để bụi mịn, tránh tình trạng tái nhiễm bẩn trong quá trình đánh bóng.
- Đối với các vết bẩn cứng đầu (dầu mỡ, xi măng, vôi), cần xử lý sơ bộ bằng dung dịch tẩy rửa chuyên dụng phù hợp với từng loại gạch và loại vết bẩn.
Kỹ thuật đánh bóng thô
- Sử dụng đĩa mài kim cương hoặc giấy nhám cỡ hạt 80-120 gắn vào máy đánh bóng, điều chỉnh tốc độ máy ở mức 1200-1500 vòng/phút.
- Áp dụng lực đều đặn từ 3-5kg/cm² và di chuyển máy theo hướng vân gạch để đảm bảo mài phẳng và đồng đều bề mặt.
- Chia khu vực sàn thành các ô nhỏ khoảng 2m x 2m và thực hiện đánh bóng theo từng ô để đảm bảo độ đồng đều.
- Trong quá trình đánh bóng, cần kiểm soát nhiệt độ bề mặt không vượt quá 40°C để tránh làm nứt gạch. Nếu phát hiện bề mặt quá nóng, có thể phun nhẹ một lượng nước để làm mát (khoảng 0,5 lít/phút).
Kiểm tra sau đánh bóng thô
- Sau mỗi lần hoàn thành một khu vực, cần lau sạch bề mặt và dùng đèn LED cường độ cao (≥1000 Lux) chiếu theo góc để kiểm tra độ phẳng và đồng đều.
- Các vết xước lớn hoặc vùng chưa đánh bóng đồng đều cần được đánh dấu và xử lý lại trước khi chuyển sang công đoạn tiếp theo.
Đánh bóng trung bình
Kỹ thuật nâng cao độ mịn
- Chuyển sang sử dụng giấy nhám mịn hơn với cỡ hạt 240-400, điều chỉnh tốc độ máy đánh bóng xuống 1000-1200 vòng/phút để kiểm soát tốt hơn và tránh làm quá nhiệt bề mặt.
- Áp dụng mô hình đánh bóng theo hình lưới đan chéo (đầu tiên theo chiều dọc, sau đó theo chiều ngang) để đảm bảo độ đồng đều tuyệt đối trên toàn bộ bề mặt.
- Kiểm soát chặt chẽ độ ẩm môi trường làm việc (≤60%) và bổ sung nước làm mát đều đặn ở mức 0,5 lít/phút để giảm thiểu bụi và tối ưu hóa hiệu quả đánh bóng.
Xử lý các vùng khó tiếp cận
- Đối với các góc, cạnh và khu vực máy đánh bóng không tiếp cận được, sử dụng dụng cụ đánh bóng cầm tay kết hợp với giấy nhám cỡ tương đương.
- Di chuyển theo hình tròn nhỏ và duy trì áp lực đều đặn để tạo độ mịn tương đương với bề mặt chính.
- Đảm bảo không bỏ sót bất kỳ vùng nào, đặc biệt là các khu vực giao nhau giữa các viên gạch.
Đánh giá chất lượng trung gian
- Sau khi hoàn thành đánh bóng trung bình, rửa sạch bề mặt bằng nước sạch và để khô hoàn toàn.
- Kiểm tra bằng cách chạm tay để cảm nhận độ mịn đồng đều và quan sát dưới ánh sáng chéo để phát hiện các vết xước còn sót lại.
- Đo và ghi nhận độ bóng trung gian bằng máy đo độ bóng góc 60° tại nhiều điểm khác nhau trên bề mặt sàn.
Đánh bóng tinh
Kỹ thuật đánh bóng tinh cao cấp
- Sử dụng hạt khô men nhung cao cấp hoặc bánh mài đất tảo với áp lực nhẹ hơn so với các bước trước, nhằm tạo ra bề mặt cực kỳ mịn và bóng sâu.
- Giảm tốc độ máy xuống còn 800-1000 vòng/phút để đảm bảo kiểm soát tối đa và tránh làm tổn hại bề mặt đã được làm mịn.
- Đối với gạch porcelain và ceramic, nên áp dụng phương pháp đánh bóng khô kết hợp với chất đánh bóng nano chứa hạt oxit nhôm kích thước dưới 10nm để lấp đầy các lỗ rỗng siêu nhỏ trên bề mặt gạch.
- Với đá tự nhiên, sử dụng dung dịch đánh bóng chuyên dụng như EW22TOUGH hoặc dung dịch GMP 0163 Florbrite để tạo lớp bảo vệ và nâng cao độ bóng.
Phủ bóng hoàn thiện
- Lau sạch hoàn toàn bề mặt sau quá trình đánh bóng và chờ khô hoàn toàn (khoảng 1 giờ) trước khi tiến hành phủ bóng.
- Phủ lớp bảo vệ đầu tiên và chờ khoảng 1 giờ để khô. Sau đó tiến hành phủ bóng lần 1, 2 và 3 với thời gian chờ giữa các lớp là 1 giờ.
- Đối với khu vực có mật độ sử dụng cao, nên áp dụng 3-4 lớp phủ bóng, trong khi các khu vực thông thường có thể sử dụng 2 lớp để giữ độ bám dính và độ bóng tự nhiên.
- Sử dụng dung dịch phủ bóng chuyên dụng như dung dịch phủ bóng GMP 0203 Tilecon Seal cho gạch ceramic hoặc GMP 0283 Superior cho đá tự nhiên với định lượng khoảng 15-20ml/m².
Hoàn thiện và bảo vệ khe gạch
- Sau khi hoàn thành đánh bóng và phủ bóng, tiến hành xử lý và bảo vệ khe gạch bằng dung dịch chống thấm chuyên dụng.
- Đối với khu vực có nguy cơ thấm nước cao như nhà tắm hoặc khu vực ngoài trời, nên sử dụng dung dịch chống thấm gốc silicone để bảo vệ khe gạch.
- Đảm bảo toàn bộ sàn được bảo vệ đồng đều, bao gồm cả khu vực khe gạch, để tránh tình trạng thấm nước và ố vàng trong tương lai.
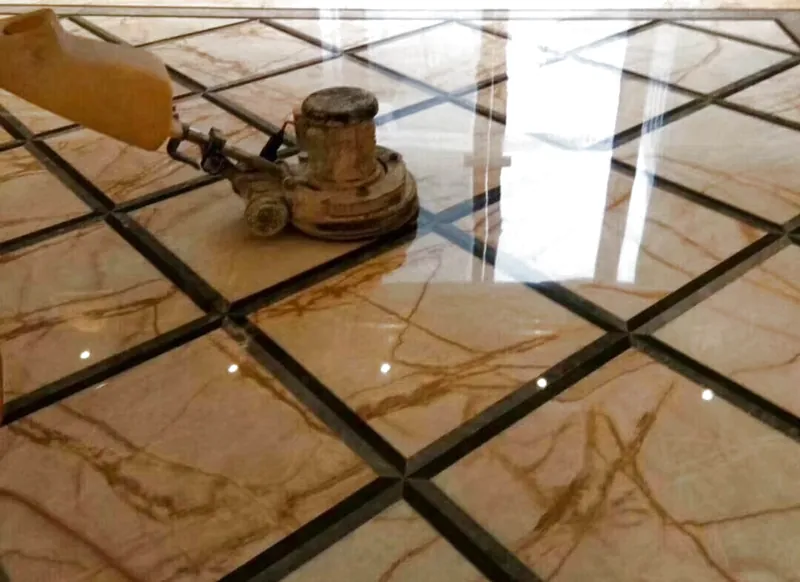
KIỂM TRA CHẤT LƯỢNG ĐÁNH BÓNG GẠCH LÁT NỀN
Kiểm tra chất lượng là bước đặc biệt quan trọng trong quy trình đánh bóng gạch lát nền, đảm bảo kết quả cuối cùng đáp ứng hoặc vượt qua tiêu chuẩn ngành và mong đợi của khách hàng. Quy trình kiểm tra đa chiều không chỉ xác nhận độ hoàn thiện về mặt thẩm mỹ mà còn đảm bảo độ bền và tính thực tiễn của bề mặt sàn trong suốt vòng đời sử dụng.
Kiểm tra cảm quan
Đánh giá độ bóng và đồng đều
- Sử dụng đèn LED cường độ cao (≥1000 Lux) chiếu theo góc 45° so với bề mặt sàn để phát hiện bất kỳ vùng nào có độ bóng không đồng đều hoặc khuyết tật nhỏ không thể thấy bằng mắt thường.
- Kiểm tra sự phản chiếu ánh sáng trên bề mặt gạch: hình ảnh phản chiếu phải rõ nét, không bị méo mó và có độ sắc nét đồng đều trên toàn bộ khu vực đã đánh bóng.
- Thực hiện kiểm tra “mẫu sàn thử” bằng cách chọn ngẫu nhiên và lắp đặt tạm thời 1m² gạch đã đánh bóng để đánh giá tổng thể về màu sắc và độ đồng nhất của độ bóng trước khi hoàn thiện toàn bộ dự án.
Kiểm tra bề mặt dưới các điều kiện ánh sáng khác nhau
- Tiến hành kiểm tra trong ba điều kiện ánh sáng: ánh sáng tự nhiên ban ngày, ánh sáng nhân tạo (đèn LED/huỳnh quang), và ánh sáng chiếu xiên góc thấp để phát hiện các vết xước vi mô3.
- Sử dụng hộp ánh sáng trung tính (khoảng 6000-6500K) để đánh giá màu sắc và độ đồng đều của bề mặt, đặc biệt quan trọng đối với gạch porcelain và gạch men màu đậm.
- Kiểm tra dưới các điều kiện ánh sáng mạnh (≥300 lux) để phát hiện các vết xước nhỏ, vết mờ hoặc khu vực chưa được đánh bóng hoàn chỉnh.
Đánh giá độ phẳng và khuyết tật bề mặt
- Sử dụng thước thủy chính xác 2m để kiểm tra độ phẳng của bề mặt sau khi đánh bóng, sai số cho phép không quá 2mm/2m chiều dài để đảm bảo thẩm mỹ và an toàn khi sử dụng.
- Kiểm tra toàn bộ bề mặt sàn để phát hiện các khuyết tật như vết nứt, sứt mẻ, bong tróc men, đốm màu bất thường hoặc các vùng có độ bóng không đều.
- Đối với các khu vực góc, cạnh, và tiếp giáp với tường hoặc đồ nội thất cố định, cần kiểm tra kỹ lưỡng hơn vì đây thường là những vị trí dễ bị bỏ sót trong quá trình đánh bóng.
Kiểm tra bằng thiết bị chuyên dụng
Đo độ bóng bề mặt
- Sử dụng máy đo độ bóng góc 60° tiêu chuẩn ngành để đánh giá định lượng độ bóng của bề mặt đã hoàn thiện, đảm bảo độ bóng đạt tối thiểu 90GU (Gloss Unit) đối với khu vực cần độ bóng cao, và mức 70-80GU đối với khu vực yêu cầu độ bóng vừa phải.
- Tiến hành đo tối thiểu 5 điểm trên mỗi 10m² diện tích sàn để đảm bảo tính đại diện của kết quả, sai số giữa các điểm không được vượt quá ±2GU để đảm bảo độ đồng đều.
- So sánh kết quả đo với tiêu chuẩn đã thỏa thuận với khách hàng và tiêu chuẩn ngành cho gạch ceramic trong nước, hoặc ISO 10545 cho tiêu chuẩn quốc tế.
Đo độ nhám bề mặt
- Sử dụng máy đo độ nhám bề mặt (Surface Roughness Tester) với chiều dài đo 5,6mm theo tiêu chuẩn DIN EN ISO 4288 để xác định chỉ số Ra (độ nhám trung bình) của bề mặt đã đánh bóng.
- Giá trị Ra lý tưởng cho bề mặt gạch đã đánh bóng nên dưới 0,1μm đối với gạch porcelain cao cấp, dưới 0,2μm đối với gạch ceramic thông thường, đảm bảo cả độ bóng và khả năng chống trượt.
- Thực hiện đo theo nhiều hướng khác nhau (dọc, ngang, chéo) để đánh giá toàn diện độ nhám bề mặt, đặc biệt quan trọng đối với các khu vực có mật độ đi lại cao như sảnh, hành lang.
Đánh giá độ cứng và độ bền
- Kiểm tra độ cứng bề mặt sau đánh bóng bằng bộ dụng cụ đo thang Mohs, đảm bảo bề mặt đạt mức tối thiểu 5 trên thang Mohs để có khả năng chống xước và mài mòn tốt.
- Thực hiện thử nghiệm độ bền chống trầy xước bằng cách sử dụng vật liệu chuẩn có độ cứng Mohs 7 (thạch anh) để kiểm tra khả năng chịu mài mòn của bề mặt gạch sau đánh bóng.
- Đối với khu vực thương mại hoặc công cộng, bổ sung thử nghiệm độ chống trượt để đảm bảo hệ số ma sát động (DCOF) đạt tối thiểu 0,42 theo tiêu chuẩn ANSI A137.1, đảm bảo an toàn cho người sử dụng.
Kiểm tra độ bền màu và độ chống bẩn
- Tiến hành thử nghiệm độ kháng bẩn bằng cách áp dụng các chất gây bẩn phổ biến (cà phê, dầu oliu, mực đánh dấu) lên bề mặt đã đánh bóng, để trong 24 giờ, sau đó làm sạch và đánh giá theo thang điểm từ 1-5 (5: làm sạch hoàn toàn bằng nước; 1: không thể làm sạch).
- Đánh giá độ bền màu dưới tác động của ánh sáng mặt trời bằng cách so sánh mẫu đã tiếp xúc với ánh nắng trong 100 giờ với mẫu đối chứng, sử dụng thiết bị so màu chuyên dụng để phát hiện sự sai lệch màu sắc.
- Thử nghiệm khả năng chống hóa chất bằng cách tiếp xúc bề mặt gạch với các dung dịch hóa học phổ biến trong gia đình (axit citric, chlorine, ammonium chloride) theo tiêu chuẩn ISO 10545-13, đánh giá bất kỳ thay đổi nào về độ bóng hoặc màu sắc sau thử nghiệm.
Kiểm tra cảm quan chuyên nghiệp
Đánh giá bằng xúc giác
- Bề mặt phải đạt độ mịn cấp “nhung” (velvet-grade), không có cảm giác hạt khi chạm tay, tạo cảm giác trơn mịn tuyệt đối khi lướt tay trên bề mặt.
- Thực hiện kiểm tra bằng lòng bàn tay ẩm và khô để đánh giá độ mịn và cảm giác khi tiếp xúc, đặc biệt là sự khác biệt giữa bề mặt đã đánh bóng và chưa đánh bóng.
- Sử dụng ngón tay (đeo găng tay cotton sạch) để kiểm tra các vùng tiếp giáp giữa các viên gạch, đảm bảo không có cạnh sắc hoặc chênh lệch độ cao gây khó chịu khi chạm vào.
Kiểm tra âm thanh
- Gõ nhẹ lên bề mặt gạch bằng vật cứng không sắc nhọn (như cán nhỏ của búa cao su) để phát hiện các khu vực bị rỗng hoặc không bám dính tốt với nền, biểu hiện qua âm thanh rỗng khác biệt.
- Thực hiện kiểm tra này trên toàn bộ diện tích sàn theo mô hình lưới 50cm x 50cm để đảm bảo không bỏ sót bất kỳ khu vực có vấn đề nào.
- Lưu ý các vùng tiếp giáp với tường, cột hoặc vị trí có đường ống đi qua, đây thường là những điểm dễ xuất hiện hiện tượng gạch không bám dính tốt với nền.
Kiểm tra độ thấm nước
- Nhỏ vài giọt nước lên bề mặt đã đánh bóng và theo dõi khả năng hút nước: bề mặt hoàn thiện tốt phải có khả năng chống thấm cao, nước đọng thành giọt tròn trên bề mặt và không thấm vào trong vòng 30 phút.
- Đánh giá thời gian khô của nước trên bề mặt gạch – bề mặt được đánh bóng và xử lý tốt sẽ có thời gian khô nhanh hơn so với bề mặt chưa được xử lý.
- Kiểm tra khe gạch bằng cách nhỏ nước có màu (thêm vài giọt mực) để đảm bảo chất lấp khe và chất chống thấm đã được áp dụng hiệu quả, không có hiện tượng thấm nước qua khe.
Đánh giá chất lượng dài hạn
Kiểm tra độ bền lớp phủ bóng
- Sử dụng phương pháp thử nghiệm băng dính: dán một mảnh băng dính chất lượng cao lên bề mặt đã được đánh bóng và phủ bảo vệ, sau đó gỡ băng dính ra một cách nhanh chóng. Lớp phủ bóng chất lượng cao sẽ không bị bong tróc theo băng dính1.
- Thực hiện kiểm tra độ bám dính của lớp phủ bằng cách sử dụng dụng cụ đo độ bám dính cross-hatch (thường dùng trong ngành sơn), đánh giá theo thang điểm từ 0-5 (0: hoàn hảo, 5: bong tróc hoàn toàn).
- Đối với các khu vực công cộng hoặc thương mại, tiến hành thử nghiệm mô phỏng mài mòn bằng cách sử dụng thiết bị mô phỏng đi lại (foot traffic simulator) với 1000-5000 chu kỳ, sau đó đánh giá sự thay đổi về độ bóng.
Đánh giá khả năng chống bẩn lâu dài
- Theo dõi hiệu suất chống bẩn tại các khu vực có mật độ sử dụng cao như lối đi, khu vực bếp, hoặc phòng tắm sau 30, 60 và 90 ngày sử dụng để đánh giá hiệu quả của lớp hoàn thiện.
- So sánh độ bóng tại các khu vực có mật độ đi lại khác nhau để xác định tốc độ mất độ bóng, từ đó lập kế hoạch bảo trì định kỳ phù hợp.
- Đối với các dự án quy mô lớn, thiết lập khu vực kiểm soát (control area) được đánh bóng và bảo vệ theo quy trình tiêu chuẩn, sử dụng làm chuẩn so sánh với các khu vực khác trong suốt thời gian sử dụng.
Kiểm tra an toàn và tuân thủ
- Đánh giá hệ số ma sát động (DCOF) của bề mặt đã đánh bóng bằng thiết bị BOT-3000E hoặc tương đương, đảm bảo đạt mức tối thiểu 0,42 cho khu vực khô và 0,60 cho khu vực ẩm ướt theo tiêu chuẩn ANSI A137.
- Kiểm tra sự tuân thủ các quy định về VOC (hợp chất hữu cơ bay hơi) của các sản phẩm sử dụng trong quá trình đánh bóng và phủ bảo vệ, đảm bảo an toàn cho sức khỏe người sử dụng.
- Đối với các công trình công cộng, thực hiện thêm thử nghiệm chống cháy và khả năng chịu nhiệt của bề mặt sàn đã hoàn thiện theo quy định hiện hành về phòng cháy chữa cháy (PCCC) của Việt Nam.
Lập hồ sơ và báo cáo chất lượng
Tài liệu hóa quy trình kiểm tra
- Lập hồ sơ chi tiết ghi lại toàn bộ quy trình kiểm tra, bao gồm phương pháp kiểm tra, thiết bị sử dụng, điều kiện môi trường khi kiểm tra (nhiệt độ, độ ẩm), và nhân viên thực hiện kiểm tra.
- Chụp ảnh “trước-sau” tại các vị trí đại diện và các khu vực từng có vấn đề để minh họa kết quả đạt được sau quá trình đánh bóng, sử dụng ảnh chụp độ phân giải cao dưới cùng điều kiện ánh sáng.
- Đánh dấu vị trí các điểm đo độ bóng, độ nhám trên bản vẽ mặt bằng để thuận tiện cho việc theo dõi và bảo trì trong tương lai.
Báo cáo kết quả cho khách hàng
- Soạn thảo báo cáo chi tiết về kết quả kiểm tra chất lượng, bao gồm các số liệu đo lường (độ bóng, độ nhám, độ cứng), kết quả kiểm tra cảm quan, và đánh giá tổng thể về chất lượng công việc.
- Tổng hợp các khuyến nghị bảo trì và vệ sinh định kỳ dựa trên kết quả kiểm tra, điều kiện sử dụng thực tế, và loại gạch/đá đã được đánh bóng.
- Cung cấp giấy chứng nhận hoàn thành công việc với các thông số kỹ thuật đạt được, bảo hành áp dụng, và lịch bảo trì đề xuất, tạo sự an tâm và tin cậy cho khách hàng.
XỬ LÝ CÁC VẤN ĐỀ TRONG QUÁ TRÌNH ĐÁNH BÓNG GẠCH LÁT NỀN
Quá trình đánh bóng gạch lát nền thường gặp một số vấn đề đặc trưng, nhưng với kinh nghiệm từ các chuyên gia dịch vụ đánh bóng gạch lát nền, chúng ta có thể khắc phục hiệu quả.
Đánh bóng không đều
Nguyên nhân chính
- Dao động áp lực không ổn định trong quá trình đánh bóng, tạo ra các vùng có độ bóng khác nhau trên cùng một bề mặt gạch.
- Trình tự sử dụng cỡ hạt giấy nhám không phù hợp, như việc bỏ qua các kích thước trung gian (ví dụ: chuyển từ 80 thẳng lên 400 mà không qua 240).
- Thiết bị đánh bóng không được bảo trì đúng cách, dẫn đến dao động tốc độ quay và áp lực không đồng đều.
- Tốc độ di chuyển máy đánh bóng không nhất quán, tạo ra các vùng được đánh bóng với thời gian tiếp xúc khác nhau.
Giải pháp hiệu quả
- Hiệu chuẩn van áp lực thiết bị đánh bóng, đảm bảo duy trì áp lực ổn định ở mức 3-5kg/cm² trong suốt quá trình làm việc.
- Tuân thủ nghiêm ngặt trình tự cỡ hạt giấy nhám theo thứ tự tăng dần: 80→120→240→400, không bỏ qua bất kỳ bước nào.
- Sử dụng thiết bị đo áp lực kỹ thuật số gắn trên máy đánh bóng với độ chính xác ±0,2kg/cm² để đảm bảo độ đồng đều.
- Chia sàn thành các ô vuông 2m x 2m và sử dụng bộ đếm thời gian để đảm bảo mỗi ô được đánh bóng trong cùng một khoảng thời gian.
Ví dụ thực tế: Tại một trung tâm thương mại ở Quận 1, Thành phố Hồ Chí Minh, việc đánh bóng 500m² sàn gạch porcelain cho kết quả không đồng đều với độ bóng dao động từ 70-95GU. Sau khi áp dụng hệ thống kiểm soát áp lực tự động và tuân thủ trình tự giấy nhám chuẩn, độ bóng đã được cân bằng ở mức 90-95GU trên toàn bộ diện tích, nâng cao giá trị thẩm mỹ và tính chuyên nghiệp của không gian.
Sai lệch màu men gạch
Nguyên nhân phổ biến
- Sự khác biệt giữa các lô vật liệu gạch, đặc biệt là khi sử dụng gạch từ các đợt sản xuất khác nhau.
- Lỗi kiểm soát nhiệt độ trong quá trình đánh bóng, làm thay đổi đặc tính màu sắc của men gạch.
- Sử dụng dung dịch tẩy rửa có tính axit hoặc kiềm mạnh trước khi đánh bóng, ảnh hưởng đến tông màu của gạch.
- Phản ứng hóa học giữa các chất đánh bóng với thành phần đặc biệt trong men gạch nhập khẩu từ châu Âu hoặc Nhật Bản.
Giải pháp chuyên nghiệp
- Sử dụng vật liệu từ cùng một lô sản xuất, lưu trữ thông tin mã lô và ngày sản xuất để đảm bảo tính đồng nhất.
- Lắp đặt hệ thống làm mát nhiệt độ ổn định với bộ cảm biến nhiệt hồng ngoại, duy trì nhiệt độ bề mặt ở mức 35-40°C trong suốt quá trình đánh bóng.
- Thực hiện thử nghiệm tương thích giữa dung dịch đánh bóng và từng loại men gạch trên một diện tích nhỏ (30cm x 30cm) trước khi áp dụng toàn diện.
- Đối với gạch nhập khẩu cao cấp, sử dụng dung dịch đánh bóng pH trung tính (6.5-7.5) được chứng nhận tương thích với các loại men đặc biệt.
Ví dụ thực tế: Khi tiến hành đánh bóng sàn gạch cho một khách sạn 5 sao tại Đà Nẵng, đội kỹ thuật đã gặp phải tình trạng sai lệch màu trên gạch porcelain nhập khẩu từ Ý. Qua phân tích, nguyên nhân được xác định là nhiệt độ cao (trên 55°C) phát sinh trong quá trình đánh bóng. Sau khi áp dụng hệ thống làm mát bằng nước chuyên dụng với lưu lượng 0,5L/phút và kiểm soát nhiệt độ dưới 40°C, vấn đề đã được khắc phục hoàn toàn, đảm bảo màu sắc đồng nhất trên toàn bộ diện tích 1.200m².
Mẻ cạnh gạch
Nguyên nhân kỹ thuật
- Độ lệch góc của đầu đánh bóng vượt quá 5° so với bề mặt gạch, tạo áp lực không đều lên cạnh gạch.
- Kỹ thuật vận hành máy không đúng, đặc biệt là khi di chuyển giữa các viên gạch hoặc thay đổi hướng đột ngột.
- Lựa chọn thiết bị đánh bóng quá nặng hoặc công suất quá mạnh cho loại gạch có độ cứng thấp.
- Các viên gạch không được lắp đặt đúng kỹ thuật, tạo ra điểm yếu tại các cạnh gạch.
Giải pháp tối ưu
- Điều chỉnh góc nghiêng của máy đánh bóng về mức 0-3° để đảm bảo áp lực đồng đều trên toàn bộ bề mặt tiếp xúc.
- Bổ sung bộ gá bảo vệ cạnh cho máy đánh bóng, tạo vùng đệm an toàn giữa đầu đánh bóng và cạnh gạch1.
- Đào tạo kỹ thuật viên về phương pháp di chuyển máy theo đường thẳng, tránh các chuyển động xoay đột ngột tại vị trí cạnh gạch.
- Trước khi đánh bóng, kiểm tra và xử lý các viên gạch lỏng lẻo bằng kỹ thuật gõ nhẹ để phát hiện âm thanh rỗng.
Ví dụ thực tế: Tại một dự án chung cư cao cấp ở Hà Nội, tỷ lệ mẻ cạnh gạch trong quá trình đánh bóng ban đầu lên đến 12% (khoảng 45 viên trên tổng số 375 viên trong khu vực thử nghiệm). Sau khi áp dụng bộ gá bảo vệ cạnh thiết kế riêng và điều chỉnh góc nghiêng máy xuống 2°, tỷ lệ mẻ cạnh giảm xuống còn dưới 1%, tiết kiệm chi phí thay thế gạch khoảng 35 triệu đồng cho toàn dự án.
ĐÁNH GIÁ RỦI RO VÀ BIỆN PHÁP PHÒNG NGỪA
Đánh bóng gạch lát nền không chỉ là một quy trình kỹ thuật mà còn tiềm ẩn nhiều rủi ro cần được nhận diện và kiểm soát. Một hệ thống đánh giá rủi ro toàn diện không chỉ bảo vệ nhân viên và khách hàng mà còn đảm bảo chất lượng công việc, tránh thiệt hại về vật chất và uy tín doanh nghiệp.
Phương pháp đánh giá rủi ro
Quy trình đánh giá 5 bước
- Xác định các mối nguy: Liệt kê tất cả các yếu tố có thể gây hại trong quá trình đánh bóng gạch.
- Xác định đối tượng bị ảnh hưởng: Nhân viên thi công, khách hàng, người qua lại, và tài sản xung quanh.
- Đánh giá mức độ rủi ro: Sử dụng ma trận 5×5 (Mức độ nghiêm trọng x Khả năng xảy ra) để phân loại rủi ro từ thấp đến cao.
- Lập kế hoạch kiểm soát: Xác định biện pháp giảm thiểu rủi ro theo nguyên tắc ERIC (Elimination, Reduction, Isolation, Control).
- Giám sát và đánh giá lại: Thường xuyên cập nhật đánh giá rủi ro và điều chỉnh biện pháp phòng ngừa khi cần thiết.
Tài liệu hóa đánh giá rủi ro
- Xây dựng biểu mẫu đánh giá rủi ro cụ thể cho từng loại công trình (dân dụng, thương mại, công nghiệp).
- Đảm bảo tất cả nhân viên được đào tạo về quy trình đánh giá rủi ro và biết cách sử dụng các biểu mẫu.
- Lưu trữ hồ sơ đánh giá rủi ro tối thiểu 2 năm để phục vụ cho việc kiểm tra và cải tiến liên tục.
Rủi ro sức khỏe và an toàn lao động
Rủi ro hóa chất
- Sử dụng các dung dịch tẩy rửa, chất đánh bóng và dung môi có thể gây kích ứng da, mắt, đường hô hấp.
- Tiếp xúc lâu dài với một số hóa chất có thể gây bệnh nghề nghiệp như viêm da tiếp xúc, hen suyễn.
- Phơi nhiễm với silica tinh thể từ bụi đá và gạch có thể dẫn đến bệnh bụi phổi silic.
Biện pháp phòng ngừa hóa chất
- Lập danh mục hóa chất đầy đủ kèm phiếu an toàn hóa chất (MSDS) cho tất cả các sản phẩm sử dụng.
- Trang bị đầy đủ PPE phù hợp: găng tay nitrile chống hóa chất, kính bảo hộ, khẩu trang N95/P100, quần áo bảo hộ.
- Thiết lập hệ thống thông gió cưỡng bức với công suất tối thiểu 5-6 lần thay đổi không khí/giờ trong không gian làm việc kín.
- Bố trí trạm rửa mắt khẩn cấp và vòi hoa sen tẩy độc tại công trường lớn hoặc bình rửa mắt cầm tay cho các dự án nhỏ.
Rủi ro cơ học và ergonomics
- Chấn thương do nâng nhấc sai tư thế: đau lưng, thoát vị đĩa đệm khi di chuyển thiết bị nặng.
- Rối loạn cơ xương khớp do tư thế làm việc gò bó, lặp đi lặp lại khi đánh bóng thủ công.
- Tai nạn do vận hành máy móc: kẹt tay, đứt tay, điện giật khi sử dụng máy đánh bóng công suất lớn.
Biện pháp phòng ngừa chấn thương
- Áp dụng nguyên tắc nâng vật an toàn: giữ lưng thẳng, sử dụng sức mạnh chân, không xoay người khi đang nâng vật.
- Sử dụng thiết bị hỗ trợ như xe đẩy, palăng cho vật nặng trên 25kg hoặc nâng vật hai người.
- Thiết kế lịch làm việc có thời gian nghỉ ngơi định kỳ: 10 phút nghỉ sau mỗi 50 phút làm việc liên tục.
- Thực hiện các bài tập khởi động và giãn cơ trước khi bắt đầu ca làm việc.
Rủi ro trượt ngã
- Sàn ướt trong quá trình làm việc gây trượt ngã cho người lao động và người qua lại.
- Các dây điện, ống nước, thiết bị vứt bừa bãi tạo thành vật cản gây vấp ngã.
- Chênh lệch độ cao giữa các khu vực sàn tạo nguy cơ vấp ngã khi di chuyển.
Biện pháp phòng ngừa trượt ngã
- Sử dụng biển cảnh báo “Sàn ướt” và rào chắn khu vực đang thi công.
- Vệ sinh và lau khô sàn ngay sau khi hoàn thành từng phần công việc.
- Sắp xếp dây cáp, ống nước gọn gàng, sử dụng nẹp cáp để giữ dây điện dọc theo tường.
- Trang bị giày an toàn có đế chống trượt cho nhân viên thi công.
Rủi ro về vật liệu và thiết bị
Rủi ro hư hỏng thiết bị
- Quá nhiệt động cơ máy đánh bóng do sử dụng liên tục quá thời gian quy định.
- Hỏng đầu mài, đĩa đánh bóng do va đập hoặc áp lực không đều.
- Trục trặc hệ thống điện do quá tải hoặc đấu nối không đúng cách.
Biện pháp phòng ngừa hư hỏng thiết bị
- Lập lịch bảo trì thiết bị định kỳ: kiểm tra mỗi 50 giờ sử dụng hoặc 1 tháng một lần.
- Đào tạo nhân viên về cách sử dụng đúng thiết bị, nhận biết dấu hiệu thiết bị hoạt động bất thường.
- Trang bị bộ ổn áp cho thiết bị đánh bóng trong khu vực có điện áp không ổn định.
- Sử dụng bộ ngắt mạch dòng dư (RCCB) với độ nhạy ≤30mA để bảo vệ người sử dụng khỏi điện giật.
Rủi ro hư hỏng bề mặt gạch
- Sử dụng hạt mài quá thô hoặc áp lực quá mạnh gây nứt vỡ gạch.
- Nhiệt độ quá cao trong quá trình đánh bóng gây biến dạng hoặc nứt gạch.
- Sử dụng hóa chất không phù hợp gây phai màu hoặc ăn mòn bề mặt gạch.
Biện pháp phòng ngừa hư hỏng gạch
- Thực hiện thử nghiệm trên một khu vực nhỏ (1m²) trước khi tiến hành đánh bóng toàn bộ diện tích.
- Tuân thủ nghiêm ngặt khuyến cáo của nhà sản xuất về công cụ và hóa chất phù hợp cho từng loại gạch.
- Sử dụng hệ thống làm mát đồng bộ để kiểm soát nhiệt độ bề mặt không vượt quá 40°C trong quá trình đánh bóng.
- Đánh dấu và bảo vệ đặc biệt các khu vực dễ bị tổn thương như cạnh gạch, góc phòng.
Rủi ro môi trường
Rủi ro ô nhiễm không khí
- Bụi mịn phát sinh trong quá trình đánh bóng gây ô nhiễm không khí, ảnh hưởng đến người lao động và khu vực xung quanh.
- Hơi hóa chất từ dung dịch tẩy rửa và chất đánh bóng gây mùi khó chịu và có thể độc hại nếu tích tụ.
- Tiếng ồn từ máy đánh bóng ảnh hưởng đến người lao động và khu vực xung quanh.
Biện pháp kiểm soát ô nhiễm
- Sử dụng máy hút bụi công nghiệp với bộ lọc HEPA kết nối trực tiếp với máy đánh bóng.
- Lắp đặt quạt thông gió cưỡng bức hoặc cửa sổ mở để đảm bảo lưu thông không khí.
- Lên lịch làm việc vào thời điểm có ít người qua lại, đặc biệt là với khu vực thương mại.
- Sử dụng thiết bị đánh bóng có mức độ ồn thấp (≤85dB) hoặc bọc cách âm cho máy khi làm việc trong khu dân cư.
Rủi ro ô nhiễm nước thải
- Nước thải từ quá trình vệ sinh và đánh bóng chứa hóa chất và bụi gạch có thể gây ô nhiễm nguồn nước.
- Xả thải trực tiếp vào hệ thống thoát nước có thể gây tắc nghẽn và hư hỏng đường ống.
- Một số hóa chất trong nước thải có thể vượt quá ngưỡng cho phép theo quy định môi trường.
Biện pháp xử lý nước thải
- Thu gom toàn bộ nước thải bằng máy hút nước chuyên dụng, không xả trực tiếp xuống cống.
- Xử lý sơ bộ nước thải bằng cách lọc qua hệ thống lắng cặn đơn giản trước khi xả thải.
- Sử dụng các sản phẩm làm sạch và đánh bóng gốc sinh học, phân hủy nhanh khi có thể.
- Tuân thủ các quy định của địa phương về xử lý và xả thải nước thải công nghiệp.
Biện pháp phòng ngừa chung
Quy trình làm việc an toàn
- Thực hiện kiểm tra an toàn trước khi bắt đầu công việc, sử dụng danh sách kiểm tra (checklist) tiêu chuẩn.
- Thiết lập khu vực an toàn với biển cảnh báo và rào chắn rõ ràng xung quanh khu vực làm việc.
- Phân công giám sát viên an toàn cho mỗi dự án, chịu trách nhiệm kiểm tra và đảm bảo tuân thủ các biện pháp an toàn.
- Không làm việc một mình, đặc biệt khi sử dụng hóa chất nguy hiểm hoặc thiết bị điện.
Đào tạo và nâng cao nhận thức
- Tổ chức đào tạo an toàn lao động định kỳ cho tất cả nhân viên, tối thiểu 6 tháng/lần.
- Thực hiện họp an toàn ngắn (toolbox talk) 5-10 phút trước mỗi ca làm việc để nhắc nhở các rủi ro cụ thể.
- Khuyến khích nhân viên báo cáo các tình huống nguy hiểm tiềm ẩn thông qua hệ thống báo cáo sự cố và tình huống suýt xảy ra tai nạn.
- Phổ biến các bài học kinh nghiệm từ sự cố đã xảy ra trong quá khứ để tránh lặp lại.
Chuẩn bị ứng phó khẩn cấp
- Trang bị bộ sơ cứu đầy đủ tại mỗi địa điểm làm việc, bao gồm thuốc rửa mắt, thuốc bỏng và băng gạc.
- Đảm bảo ít nhất một nhân viên được đào tạo sơ cứu cơ bản có mặt tại mỗi ca làm việc.
- Lập và phổ biến quy trình ứng phó khẩn cấp, bao gồm số điện thoại cấp cứu và địa chỉ cơ sở y tế gần nhất.
- Trang bị bình chữa cháy phù hợp (loại ABC) và đảm bảo nhân viên biết cách sử dụng.
Đảm bảo an toàn khách hàng
Thông tin và hướng dẫn khách hàng
- Thông báo cho khách hàng về các rủi ro tiềm ẩn trong quá trình đánh bóng và sau khi hoàn thành.
- Hướng dẫn khách hàng về thời gian an toàn để sử dụng lại khu vực đã đánh bóng (thường 24-48 giờ).
- Cung cấp thông tin về các biện pháp chăm sóc và bảo dưỡng sàn sau đánh bóng.
- Đặt biển cảnh báo “Sàn mới đánh bóng – Cẩn thận trơn trượt” sau khi hoàn thành công việc.
Bảo vệ tài sản khách hàng
- Che phủ đồ nội thất, thiết bị và các bề mặt không cần đánh bóng bằng bạt hoặc màng phủ chuyên dụng.
- Di chuyển các vật dụng nhỏ, quý giá ra khỏi khu vực làm việc hoặc bảo quản an toàn.
- Kiểm tra và ghi lại tình trạng các vật dụng xung quanh trước khi bắt đầu công việc để tránh tranh chấp sau này.
- Sử dụng các biện pháp bảo vệ đặc biệt cho các khu vực nhạy cảm như thiết bị điện tử, hệ thống HVAC.
Kiểm soát tiếp cận
- Hạn chế người không phận sự vào khu vực đang thi công thông qua biển báo và rào chắn.
- Đối với khu vực thương mại, lên kế hoạch thi công vào thời điểm có ít người qua lại (sau giờ làm việc, cuối tuần).
- Thiết lập lối đi an toàn tạm thời nếu cần thiết để đảm bảo khách hàng có thể tiếp cận các khu vực khác.
- Trong trường hợp phải duy trì hoạt động, phân chia khu vực thi công thành nhiều phần nhỏ để luân phiên đánh bóng.
PHƯƠNG PHÁP THỰC HIỆN ĐÁNH BÓNG GẠCH LÁT NỀN
Phương pháp thực hiện là yếu tố quyết định đến hiệu quả và chất lượng của quy trình đánh bóng gạch lát nền. Một phương pháp thực hiện được thiết kế tối ưu không chỉ nâng cao hiệu quả công việc mà còn đảm bảo tính đồng đều, an toàn và tuổi thọ lâu dài cho bề mặt sàn.
Phân vùng làm việc
Phương pháp chia khu vực theo lưới
- Chia khu vực làm việc thành các ô nhỏ kích thước 2m x 2m để đảm bảo đánh bóng đồng đều và kiểm soát chất lượng hiệu quả.
- Sử dụng băng keo đặc biệt màu xanh hoặc đỏ (loại không để lại keo sau khi tháo) để đánh dấu ranh giới các vùng làm việc.
- Áp dụng quy tắc “hoàn thiện từng ô” – chỉ chuyển sang ô tiếp theo khi ô hiện tại đã được đánh bóng đạt tiêu chuẩn và được kiểm tra chất lượng.
- Đối với không gian lớn trên 100m², nên phân chia thành các khu vực lớn hơn (khoảng 20-25m²), mỗi khu vực lại được chia thành các ô nhỏ 2m x 2m để thuận tiện cho việc quản lý nhân lực và thời gian.
Trình tự thực hiện theo nguyên tắc “từ trong ra ngoài”
- Bắt đầu từ điểm xa nhất so với lối ra và di chuyển theo hướng về phía lối ra để tránh đi lại trên khu vực đã đánh bóng.
- Đối với phòng hình chữ nhật, áp dụng phương pháp “Z-pattern”: bắt đầu từ góc xa nhất, di chuyển theo hình chữ Z để đảm bảo không bỏ sót khu vực nào.
- Chia thành nhiều ca làm việc đối với công trình lớn, mỗi ca hoàn thiện một khu vực cụ thể và có biên bản bàn giao giữa các ca.
- Xử lý riêng khu vực đặc biệt (như khu vực gần cửa ra vào, khu vực có nhiều người đi lại) vào thời điểm cuối cùng để giảm thiểu nguy cơ hư hại sau khi đánh bóng.
Ví dụ thực tế: Tại một trung tâm thương mại ở Quận 7, Thành phố Hồ Chí Minh với diện tích sàn 850m², đội thi công đã chia toàn bộ khu vực thành 4 phân khu chính và áp dụng phương pháp đánh bóng theo lưới 2m x 2m. Quá trình thực hiện theo trình tự từ khu vực sâu nhất ra đến lối ra đã giúp giảm thời gian thi công từ 7 ngày xuống còn 5 ngày và nâng cao độ đồng đều của bề mặt sàn sau đánh bóng.
Quy trình làm việc theo nhóm
Phân công nhiệm vụ chuyên môn hóa
- Phân chia nhóm làm việc thành các vai trò rõ ràng: người vận hành máy đánh bóng (yêu cầu kỹ năng cao), người kiểm tra chất lượng, người hỗ trợ vật tư và xử lý vấn đề phát sinh.
- Đối với dự án lớn (trên 200m²), cần bố trí tối thiểu 4 thành viên trong nhóm: 2 người vận hành máy đánh bóng (xoay ca để đảm bảo hiệu suất), 1 người phụ trách kiểm tra chất lượng, và 1 người hỗ trợ vật tư.
- Mỗi thành viên phải được đào tạo chuyên sâu về trách nhiệm của mình và có khả năng hỗ trợ các vị trí khác khi cần thiết.
- Xây dựng ma trận kỹ năng (skill matrix) cho từng thành viên trong đội, đảm bảo mỗi kỹ năng quan trọng luôn có ít nhất 2 người thành thạo để dự phòng trong trường hợp khẩn cấp.
Hệ thống truyền thông nội bộ hiệu quả
- Thiết lập quy trình truyền thông rõ ràng giữa các thành viên trong nhóm, sử dụng bộ đàm (walkie-talkie) để liên lạc trong không gian rộng hoặc ồn ào.
- Áp dụng hệ thống báo hiệu tay (hand signals) chuẩn hóa để giao tiếp trong môi trường ồn ào khi máy đánh bóng hoạt động.
- Tổ chức họp ngắn (5-10 phút) trước khi bắt đầu ca làm việc để phổ biến kế hoạch, phân công nhiệm vụ và thảo luận các vấn đề tiềm ẩn.
- Sử dụng bảng theo dõi tiến độ trực quan (visual progress board) đặt tại hiện trường để cập nhật tình trạng từng khu vực, giúp mọi thành viên dễ dàng nắm bắt tiến độ chung.
Phối hợp liền mạch giữa các công đoạn
- Xây dựng quy trình chuyển giao công việc giữa các giai đoạn: người thực hiện đánh bóng thô bàn giao trực tiếp cho người đánh bóng trung bình, sau đó đến người đánh bóng tinh.
- Sử dụng hệ thống đánh dấu trạng thái bằng màu: Đỏ (chưa xử lý), Vàng (đang xử lý), Xanh lá (đã hoàn thành) để dễ dàng theo dõi trạng thái của từng khu vực.
- Mỗi công đoạn chuyển giao cần có biểu mẫu kiểm tra chất lượng (quality check form) được ký xác nhận bởi cả người bàn giao và người nhận.
- Duy trì khoảng cách an toàn giữa các nhóm làm việc (tối thiểu 5m) để tránh ảnh hưởng lẫn nhau, đặc biệt là giữa công đoạn đánh bóng thô (tạo nhiều bụi) và đánh bóng tinh (đòi hỏi môi trường sạch).
Ví dụ thực tế: Tại một dự án đánh bóng gạch cho khách sạn 5 sao ở Nha Trang, đội thi công 6 người được chia thành 3 cặp, mỗi cặp phụ trách một công đoạn (đánh bóng thô, trung bình và tinh). Bằng cách áp dụng quy trình làm việc theo dây chuyền và hệ thống truyền thông nội bộ hiệu quả, đội đã hoàn thành 1.200m² sàn trong 8 ngày, nhanh hơn 30% so với phương pháp truyền thống và đạt độ bóng đồng đều 95GU trên toàn bộ diện tích.
Kỹ thuật chuyên biệt cho từng loại gạch
Đánh bóng gạch ceramic
- Sử dụng phương pháp đánh bóng ướt với lưu lượng nước vừa phải (0,3-0,5 lít/phút) để giảm nhiệt độ và tránh nứt men gạch.
- Áp dụng áp lực nhẹ hơn (2-3kg/cm²) so với gạch porcelain vì gạch ceramic có độ cứng thấp hơn.
- Giới hạn tốc độ máy đánh bóng ở mức 1000-1200 vòng/phút để tránh quá nhiệt trên bề mặt men.
- Chuyển đổi giữa các cỡ hạt mài mịn hơn (80→180→320→600) để tạo độ bóng mịn mà không làm tổn hại đến lớp men.
Đánh bóng gạch porcelain
- Áp dụng phương pháp đánh bóng khô kết hợp với hút bụi công nghiệp, đặc biệt hiệu quả với gạch porcelain không tráng men.
- Có thể sử dụng áp lực cao hơn (4-5kg/cm²) nhờ độ cứng vượt trội của gạch porcelain.
- Tốc độ máy có thể điều chỉnh lên cao hơn (1300-1500 vòng/phút) trong giai đoạn đánh bóng thô.
- Sử dụng hạt đánh bóng kim cương chuyên dụng để đạt hiệu quả tối ưu, theo trình tự: 50→100→200→400→800→1500→3000 grit.
Đánh bóng đá tự nhiên (marble, granite)
- Thực hiện phương pháp đánh bóng ướt bắt buộc với lưu lượng nước cao hơn (0,8-1 lít/phút) để làm mát và bảo vệ bề mặt đá.
- Điều chỉnh áp lực theo từng loại đá: đá marble (2-3kg/cm²), đá granite (4-6kg/cm²).
- Đối với đá marble, cần sử dụng phụ gia chống ố vàng trong nước làm mát (tỷ lệ 1:300).
- Áp dụng kỹ thuật “step-polishing” (đánh bóng từng bước): mỗi khu vực được đánh bóng lặp lại 2-3 lần với cùng một cỡ hạt trước khi chuyển sang cỡ hạt mịn hơn.
Ví dụ thực tế: Khi thực hiện đánh bóng 200m² sàn gạch porcelain cao cấp tại một biệt thự ở Phú Mỹ Hưng, đội kỹ thuật đã áp dụng phương pháp đánh bóng khô kết hợp với hệ thống hút bụi công nghiệp công suất 2500W. Quá trình đánh bóng được thực hiện theo 7 bước với các hạt kim cương từ 50 đến 3000 grit. Kết quả đạt được là bề mặt sàn có độ bóng 98GU, cao hơn 15% so với tiêu chuẩn yêu cầu ban đầu và tuổi thọ độ bóng kéo dài đến 5 năm mà không cần bảo dưỡng lớn.
Xử lý các trường hợp đặc biệt
Khu vực góc cạnh và khó tiếp cận
- Sử dụng máy đánh bóng cầm tay mini với đầu mài phù hợp cho các góc nhỏ và khu vực máy lớn không tiếp cận được.
- Áp dụng kỹ thuật “góc kép” (double angle): đánh bóng từ hai hướng khác nhau để đảm bảo không bỏ sót góc nào.
- Đối với khu vực sát tường, sử dụng máy đánh bóng có đầu mài điều chỉnh góc (swivel head) giúp tiếp cận sát mép và góc.
- Khu vực dưới đồ nội thất cố định cần sử dụng đầu mài dạng đĩa mỏng (thin disk) với độ dày dưới 10mm để có thể luồn vào không gian hẹp.
Xử lý khu vực bị hư hỏng nặng
- Đối với vùng gạch bị nứt hoặc vỡ, thực hiện kỹ thuật “cắt và thay thế cục bộ”: cắt tỉ mỉ phần gạch hư hỏng và thay thế bằng miếng gạch mới có cùng màu sắc, kết cấu.
- Với khu vực bị ố vàng sâu, áp dụng phương pháp “phục hồi theo lớp”: đánh bóng thô với áp lực cao hơn 15-20% để loại bỏ hoàn toàn lớp bề mặt bị ố.
- Trường hợp gạch bị mất màu do tác động của hóa chất, sử dụng kỹ thuật “phục hồi màu” kết hợp với chất phủ bảo vệ đặc biệt chứa pigment phù hợp.
- Khu vực gạch bị bong tróc cần được xử lý với kỹ thuật “neo hóa học”: bơm keo epoxy đặc biệt vào dưới viên gạch để cố định trước khi tiến hành đánh bóng.
Xử lý các loại vết bẩn cứng đầu
- Vết rỉ sét: sử dụng dung dịch axit oxalic chuyên dụng (nồng độ 5-10%) kết hợp kỹ thuật “đánh bóng khoan tâm” – tập trung xử lý từ tâm vết bẩn và mở rộng dần ra ngoài.
- Vết xi măng: dùng dung dịch axit phosphoric nồng độ thấp (3-5%) và kỹ thuật “ngâm có kiểm soát” – để dung dịch tác động trong thời gian ngắn (3-5 phút) và giám sát liên tục.
- Vết keo silicon: áp dụng kỹ thuật “đông-cạo-mài” – làm đông keo bằng đá khô CO₂, cạo bỏ phần chính, sau đó mài nhẹ để loại bỏ phần còn lại.
- Vết sơn: kết hợp dung môi hữu cơ phù hợp (như acetone hoặc MEK) với kỹ thuật “bọc-ngâm” – sử dụng vải thấm dung môi bọc kín vùng bị dính sơn trong 15-20 phút trước khi cạo bỏ.
Ví dụ thực tế: Tại một nhà hàng ở Phố cổ Hà Nội, sàn gạch bông cổ 70 năm tuổi bị nhiều vết bẩn cứng đầu và hư hỏng cục bộ. Đội kỹ thuật đã sử dụng phương pháp “cắt và thay thế cục bộ” cho 15 viên gạch bị vỡ, kết hợp với kỹ thuật phục hồi màu cho 35 viên gạch bị phai màu. Đối với vết xi măng cứng đầu, họ áp dụng kỹ thuật “ngâm có kiểm soát” với dung dịch axit phosphoric 3%, kiểm soát chặt chẽ thời gian tác động để tránh ảnh hưởng đến màu sắc nguyên bản của gạch. Kết quả, sàn gạch bông cổ được phục hồi thành công với độ bóng đạt 75GU, vẫn giữ được vẻ đẹp hoài cổ đặc trưng.